What is Computer Numeric Control (CNC) Manufacturing
CNC Machining is a fabrication method where manufacturing is done via a series of commands written as specific coding instructions. CNC fabrication incorporates subtractive fabrication where removal of material occurs during manufacturing process vice versa to Additive Manufacturing methods, where material is constantly added to the component.
Working Principle of CNC Machines
The distinguishing feature of modern CNC machines is that CNC machines are working on the CNC instructions provided by users as digital files, encoded with machining instructions. The initial stage involves designing machinable parts in CAD software packages. Both CAD (computer aided designing) and CAM (computer aided manufacturing) processes are done using software packages like AutoCAD, Solid Works, Fusion 360 etc. which allow model preparation for fabrication and debugging of the model thus creating a complete CNC program for machining and fabrication of finished part geometry. One important part of the CAM process is to prevent any collisions between the workpiece and the tools, requiring real-time simulative assessments.
The next stage comprises of selecting correct machining parameters including cutting speed, feed rate, etc. The complete set of data is converted into the coding language of the machine, which is called G- code.
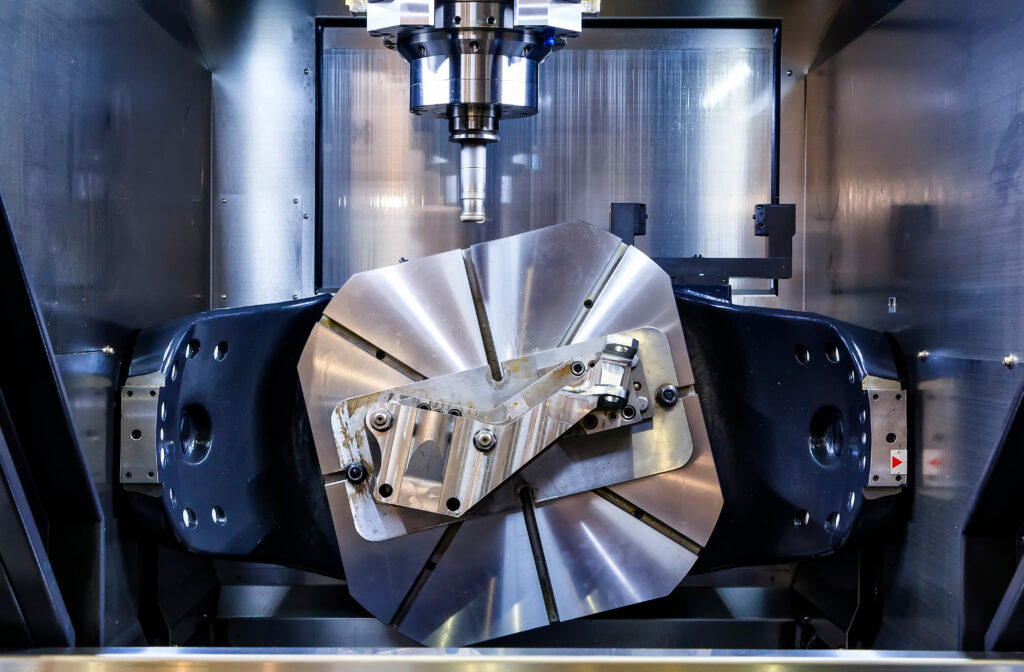
CNC Machining Processes
The automated processes which are an integral part of CNC machining comprise namely of Milling, Turning, Drilling, Grinding and various Post-Processes. These automated processes are chosen as per the requirements of the intended finished product.
CNC-Milling Operation
Milling is a universal fabrication technique which yields high accuracy and tolerances. Milling can be done on various materials. The rotation of a cutting tool is used to achieve material removal as chips when the milling tool contacts the workpiece.
Milling generally consists of End milling, Chamfer milling, face milling, drilling, boring and tapping procedures. These processes cater to manufacturing wide complex geometry ranges.
CNC-Turning Operation
The Turning process is opposite of milling in the sense that the cutting tool is moving laterally whereas the workpiece is rotated. The CNC turning operations are normally used in manufacturing of shafts. The rotating workpiece is gradually brought into contact with the moving tool to cut metal strips or bits termed as metal chips. Turning is both applicable on external or internal cylindrical surfaces.
Grinding Operation
Grinding incorporates rotating grinding wheels to achieve material removal with an objective to attain metal component’s high-end surface finishing and precision. Grinding is hence utilized for finishing operations once the workpiece has passed milling and cutting stages.
Post-Processing of Machined Parts
In order to optimize the properties of metals for a specific application, post-treatments of the machined workpieces are carried out after the CNC machining step. Heat treatments aim at improving the internal microstructure and surface treatments modify the surface of the component. Common heat treatments for steel components include stress relief annealing to relieve internal stresses by heat input. For aluminum components, anodizing is often used for hardening or optimal appearance.
CNC Machining and Production Capability
CNC machining can be used for a wide range of materials, including various metals, plastics, foams, composites and wood materials. Simple geometries are produced with three-axis milling machines, while multi-axis milling machines, especially five-axis CNC milling machines, are available for the production of complex geometric components. 3-axis CNC milling machines use three linear axes of motion, while 5-axis CNC milling machine can be used to rotate the cutting head and/or the machine bed in addition to linear motion. Multi-axis CNC machines can help increase the flexibility of the manufacturing process, but at the expense of higher costs.
Regardless of the fact that CNC machining is a fast process due to full process automation, manual machining still exists in the manufacturing sector, especially for small batches in RP rapid prototyping. CNC machining still dominates a larger part of the manufacturing market, where accuracy is essential, and key industrial sectors incorporate it as an integral part of their manufacturing process including:
- Aerospace and Aviation: This market is dominated by lightweight but durable materials like Aluminium, Nickel, Titanium and Composite Materials and complex geoemtries which often require 5-axis CNC-manufacturing with intensive quality control.
- Electrical sector: While electronic components are usually not CNC-machined, various components of the manufacturing process require tightest tolerances and are manufactured by a mix of CNC machining with processes like surface micromachining, bulk micromachining, HAR micromachining, Deposition, Lithography, Etching and Wire bonding. Common products are wafer chucks, gas distribution plates, wafer carriers, sensors like microbolometer, actuators like thermal actuators and switches like micromirror devices.
- Industrial Machines: Industrial manufacturing machines like hydraulic presses, food processing lines or injection machines require fast and reliable processes. To achieve the necessary tolerances precision components are required at various stages. From attachment points to moulds, CNC-Machining is required to manufacture high quality parts in smaller volumes at industrial machines, as investment goods are usually not built at large quantities.
- Automotive sector: A vehicle consists of many moving parts and complex assemblies. Moving parts and assemblies require high precision to maintain quality, which is why CNC manufacturing is often used. For example, internal engine surfaces, the mounts of bearings, and even contact surfaces are machined before assembly. Since the automotive industry produces vehicles in large quantities, raw parts from casting processes are often used, which are only machined on the functional surfaces in order to save costs compared to milling from the block.
On an overall basis, CNC machining has established itself in the production sector as a reliable, highly accurate and flexible manufacturing technology. However, the costs associated with the cumulative CNC machining processes are higher compared to many other manufacturing processes. Therefore, it becomes inevitable to devise such process design parameters which optimize the CNC machining process parameters thus making the overall process cost-effective.
Trends in CNC-Machining: Sharing Economy and Manufacturing Platforms
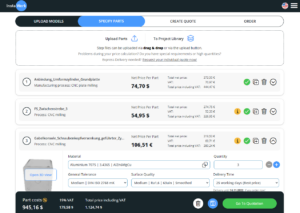
As can be seen from the previously mentioned aspects, CNC manufacturing is an essential part of many industries and is used wherever precision is required. Especially for small to medium quantities, CNC manufacturing makes sense.
However, CNC manufacturing is also associated with a high level of complexity. CAD/CAM planning is complex, multi-axis precision machines are expensive and require regular maintenance. In recent years, the effects of the shortage of skilled workers have also become increasingly apparent, as it is almost impossible to find operators for the machines.
Therefore, companies that have a need for CNC components are increasingly turning to digital procurement solutions such as InstaWerk, offering simple, cost-effective and fast procurement of CNC components, thus relieving the customer of the organizational and financial hurdles of in-house production.
Our customers can conveniently upload their CAD data to our website and receive an instant price for their components. Through digital order bundling and manufacturing in our exclusive manufacturing network, we ensure high quality and 24/7 availability.