On September 16–17, 2025, Berlin will once again become the center of European industrial strategy. The German Mechanical Engineering Summit (Maschinenbau-Gipfel) brings together leaders from engineering, manufacturing, politics, and research to address the pressing challenges of the industry.
While the event is well known in Europe, it may be less familiar in the United States. Think of it as the German equivalent of a cross between IMTS and a high-level industry policy forum – a place where business leaders and decision makers not only showcase innovation but also discuss the future of industrial competitiveness, supply chain resilience, and digital transformation.
For InstaWerk, the Summit is the ideal platform to demonstrate how digital solutions can accelerate product development, reduce costs, and ensure quality – all critical levers in a rapidly changing global manufacturing landscape.
The Context: Why 2025 Is a Turning Point for Mechanical Engineering
Mechanical engineering is under pressure worldwide.
- Geopolitical uncertainty challenges global supply chains.
- Labor shortages and the growing skills gap force companies to rethink processes.
- Cost pressures from energy, raw materials, and logistics are hitting margins.
- Digitalization and AI demand new approaches to procurement, development, and operations.
The German Summit reflects these challenges – and provides a stage for innovative answers.
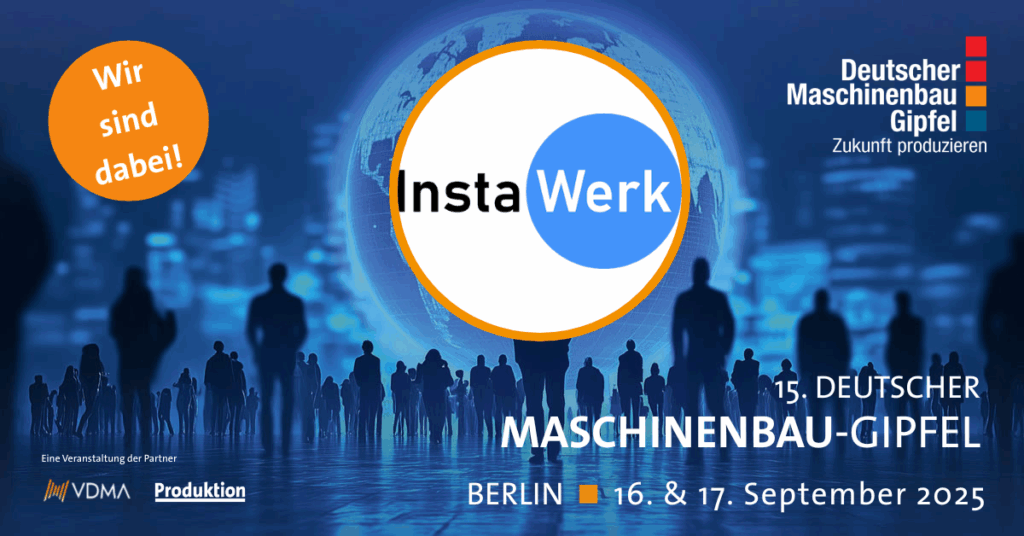
InstaWerk’s Contribution to Global Competitiveness
At InstaWerk, we believe that the next leap in competitiveness comes from digitally transforming the way companies source, develop, and validate products. Our platform directly addresses the issues that will dominate discussions in Berlin:
- Digital Procurement
We enable faster, more transparent sourcing decisions. With data-driven processes, companies can reduce risk and increase agility – essential in times of supply chain volatility. - Accelerated Product Development
Speed matters. InstaWerk shortens development cycles and helps companies bring products to market faster – turning time-to-market into a real competitive advantage. - Cost Efficiency at Scale
By streamlining development and sourcing, we help engineering-driven companies free up resources and protect their margins – without compromising flexibility. - Data-Driven, Measured Quality
Quality remains the foundation of mechanical engineering. Our approach combines digital documentation with metrological validation – creating reliability and trust in every project.
Why This Matters for U.S. Companies
Although the German Mechanical Engineering Summit is a European event, the themes resonate globally. U.S. engineers and procurement professionals face the same pressures:
- Supply chain fragility
- The push for speed and innovation
- Rising costs
- The demand for transparent, data-backed quality assurance
InstaWerk’s solutions are designed for exactly this environment – helping companies on both sides of the Atlantic adapt faster and compete more effectively.
Looking Ahead
The German Mechanical Engineering Summit 2025 is more than a conference. It is a strategic checkpoint for how one of the world’s strongest industrial sectors is preparing for the future.
InstaWerk is proud to be part of that conversation – and to bring digital procurement, accelerated product development, cost efficiency, and data-driven quality to the forefront.
👉 Learn more about the event: maschinenbau-gipfel.de