Hybrid Manufacturing: Superiority by combined Processes
The manufacturing sector has revived itself substantially with a growing interest in Hybrid Manufacturing Technologies particularly due to its capability in manufacturing products in a highly efficient manner with increased performance. Hybrid Manufacturing is a collective term which comprises of various latest developments in the manufacturing processes domain where these processes are combined and integrated with the objectives to increase design freedom, improve quality, reduce manufacturing time, thus allowing the extension in manufacturing base and areas of application.
Manufacturers incorporate a wide array of operations to produce the required products as per specifications for the industrial sector. Common manufacturing processes are Computer Numerical Control (CNC) machining, additive manufacturing, transformative processing including forming, joining, and dividing process operations particularly welding operations. In the last years these technologies have moved closer together and opened new possibilities for designers and engineers.
Each manufacturing process comes with associated drawbacks and constraints which are difficult to eliminate particularly. CNC machining due to its process complexity involves a higher degree of difficulty in the fabrication and manufacturing of complicated geometric entities pertaining to the machine tool accessibility. The scope of Additive Manufacturing technologies yet remains limited particularly due to its longer production times and lower manufacturing accuracy as compared to CNC machining methods. Development of forming processes remain restricted due to the spring back (rebound) effect and limited formability parameter of materials. It is quite challenging to regulate the dimensional accuracy of components during the welding process.
The aforementioned issues and process complications with regards to existing manufacturing systems can be resolved using hybrid manufacturing which allows integration of more than one manufacturing processes.
Here are some recent research results regarding hybrid manufacturing technologies from academia
- The Combination of the CNC machining and the Additive Manufacturing processes can yield an effective solution to existing process limitations in Additive Manufacturing pertaining to the enhanced accuracy and machining capability (rate of machining) during the process 1.
- The integration of laser-based heating and forming processes can substantially reduce the spring back (rebound) phenomenon 2.
- The combination of ultrasonic vibration and drilling process can yield a reduction in rate of tool wear 3.
- The utilization of laser drilling methodology together with Electro-chemical Machining (ECM) causes a significant reduction in the formation of recast layer (layer of resolidified material) and the heat affect zone (HAZ). HAZ is an area of metal which does not melt but rather experiences material compositional changes under the influence of high operating temperatures 4.
Lets dive deeper into two hybrid processes, which have been implemented by industry.
Hybrid Additive Manufacturing with Carbon Fiber Reinforcement
In 2018, Germany-based composite engineering company CIKONI introduced a hybrid manufacturing technology based on additive manufacturing and carbon fiber reinforcement. Most fiber-reinforced additive manufacturing processes replicate FDM technology, in which a short-fiber or long-fiber reinforcement is introduced into the plastic melt during printing 5.
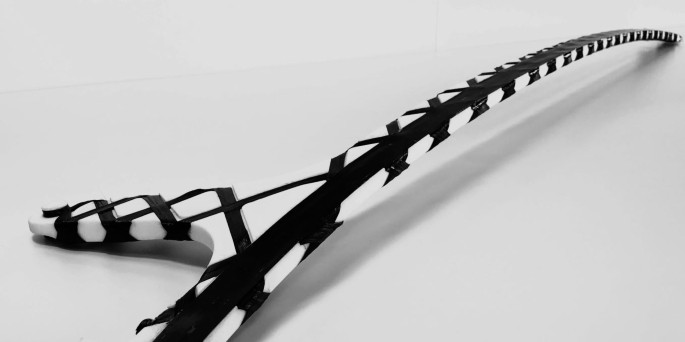
The disadvantage of these approaches is that the fiber reinforcement can only be applied in the printing plane. This can effectively provide in-plane support for compressive and tensile forces, but most components are subjected to three-dimensional loading. In addition, the cost of fiber-reinforced filaments is very high and the printing speed is low, making cost-effective manufacturing almost impossible.
In contrast, AdditiveCARBON's hybrid approach combines unreinforced 3D printing, which is cost-effective and scalable, with continuous fiber reinforcement based on the robotic winding process. The robotic guidance also allows fiber reinforcement in space so that more complex load cases can be endured.
The principle has already been successfully tested with German automaker Audi on a roof frame segment. The hybrid-manufactured component bears the underlying loads thanks to carbon fiber reinforcement. Additive manufacturing allows almost unlimited geometric design freedom.
3D Printing of Electronics by Combination with 5-Axis Machines.
5-axis milling machines are common machines for CNC machining of complex geometries from different machining directions. Optomec of Albuquerque, USA combines the degree of freedom of a 5-axis machine with the application of conductive tracks for 3D printing of electronic components.
Resistors, capacitors, antennas, sensors, and thin film transistors can thus be generated directly on a 3D surface using additive manufacturing. The process parameters of the application allow various electrical parameters, such as resistance, to be set. 3D printing of electronic components has already been implemented on plastic, metal and ceramics.
In the process, the metals are first atomized into tiny particles in an atomizer. The heated particles are then applied to the surface via a printed gas. Resolutions of up to 10 µm are possible.
The merits of Hybrid Manufacturing in terms of improved productivity via ease of manufacturing complex geometries while maintaining high efficiency and accuracy levels in comparatively shorter production time spans allows us to further grow our existing manufacturing sector’s potential in yet unexplored avenues. The management of several processes and the availability of the individual technologies in the required dimensions (size, number of pieces, quality) is challenging in hybrid processes.
Even though we at InstaWerk have specialized in CNC machining and can score here with a fast instant quoting for CNC-Machining, we will keep an eye on hybrid technologies with which we can offer our customers greater added value. Currently, InstaWerk is already able to combine CNC machining of components with extensive heat treatments and surface modifications.
Sources on Hybrid Manufacturing
- Liang, H.; Hong, H.; Svoboda, J.; A combined 3d linear and circular interpolation technique for multi-axis CNC machining. Journal of Manufacturing Science and Engineering-Transactions of the ASME, 2002.
- Duflou, J.R.: Laser assisted incremental forming formability and accuracy improvement. Cirp Annals – Manufacturing Technology, 2007.
- Heisel, U.: Ultrasonic deep hole drilling in electrolytic copper ecu 57. Cirp Annals – Manufacturing Technology, 2008.
- Zhang, H.; Xu, J.W.; Wang, J.M.: Investigation of a novel hybrid process of laser drilling assisted with jet electrochemical machining. Optics and Lasers in Engineering, 2009.
- CIKONI GmbH: Additively manufactured roof frame with local carbon fiber reinforcement, 2018.